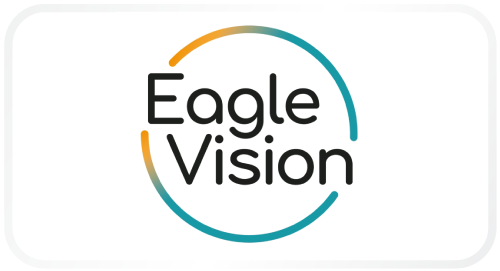
For more than 25 years, we have created powerful testing solutions for the food, beverage, and packaging industries. And as part of Industrial Physics – a global packaging, product, and material test and inspection partner – we are able to support manufacturers, production lines, and laboratories all over the world. Our unwavering focus on innovation and continuous development keeps us one step ahead of the competition. We work with some of the biggest names in industry, many of which rely on us as a “one-stop” supplier for all of their inspection needs.
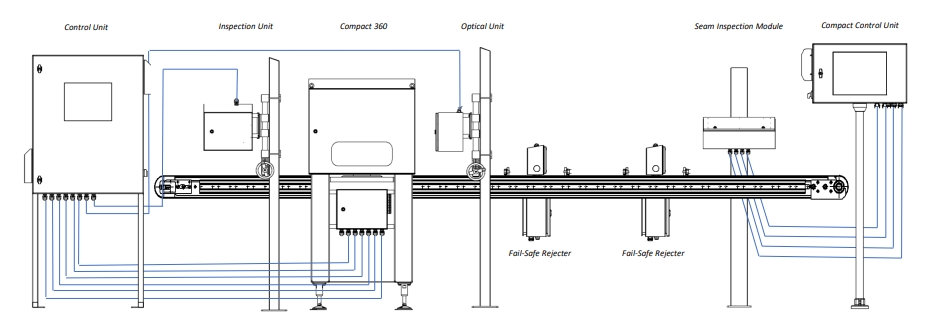
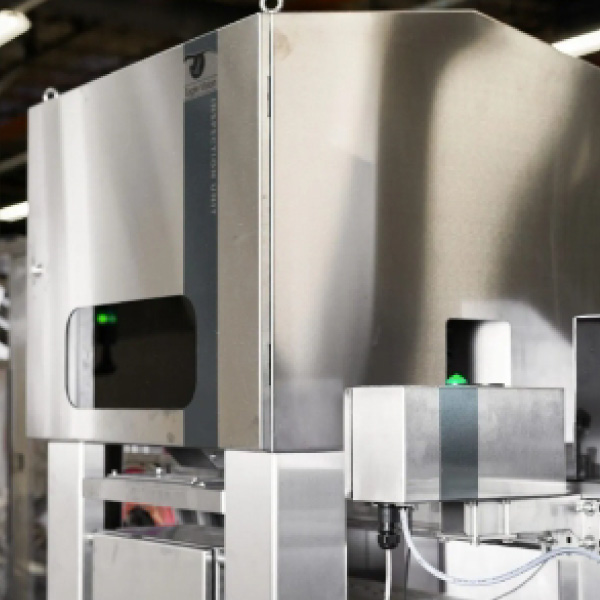
360° Can Inspection
The 360° Can Inspection module is a highly accurate, reliable and proven Mix-Up & Integrity Detection system for lithographed & labeled cans.The system can detect Barcode Reading, 2D Data Matrix Code Reading, Decoration Inspection, color print quality, ghost prints (double prints), upside-down cansincluding damages detection on the exterior of the can
Options:
OCR Code Reading, Label positioning, Empty Can Inspection (interior + flange), Seam Inspection, Cap Inspection, Code Reading of batch/date codes
Options:
OCR Code Reading, Label positioning, Empty Can Inspection (interior + flange), Seam Inspection, Cap Inspection, Code Reading of batch/date codes
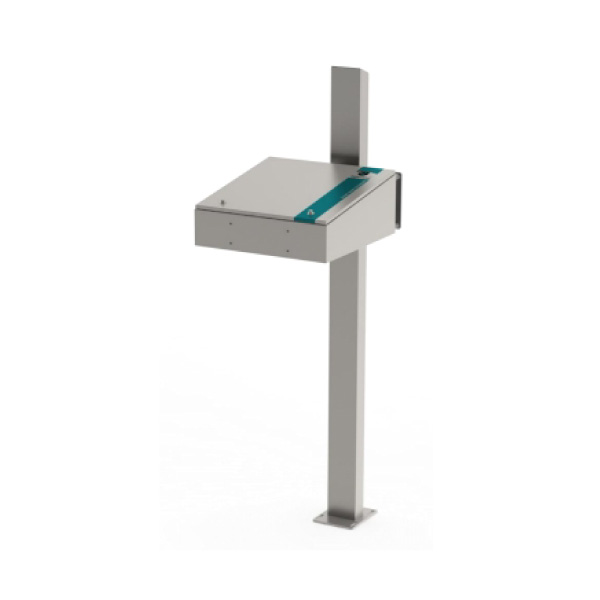
In Line Seam Inpsection
The In-line Seam Inspection module inspects the complete seam around the can. The module is positioned in-line to inspect 100% of the produced cans, non-destructively. Various can sizes and can shapes are inspected without any product handling. The inspection is available for high line speeds. Sample defects are Droops, V-shape, U-shape, Spur, Lipper, Double ends, Incomplete seam, Cut seam, Knocked down flange etc. Options: Empty Can Inspection, 360° Can Inspection, Code Reading
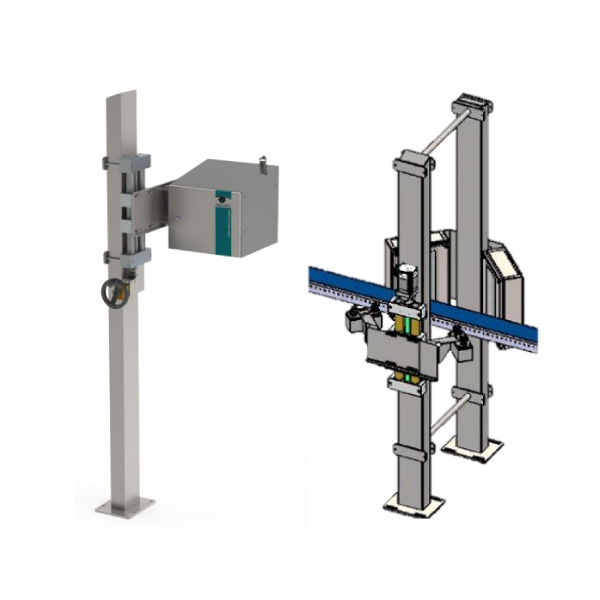
Cap Inpsection
Cap Inspection is the part of quality control for the production line. It is used for crown corks, turn/twist caps, snapcaps, easy caps and more.It helps to inspect the application;Cap Positioning (canted caps, screw caps, double caps, cap height, temper evidence, bullnose caps, flip caps)
Cap Mix-Up (color, artwork, code, embossing) Cap Orientation (aligned with the product packaging or labels)Options: (360 degree) Label Inspection, Code Reading of batch/date codes, Fill-Level Inspection
Cap Mix-Up (color, artwork, code, embossing) Cap Orientation (aligned with the product packaging or labels)Options: (360 degree) Label Inspection, Code Reading of batch/date codes, Fill-Level Inspection
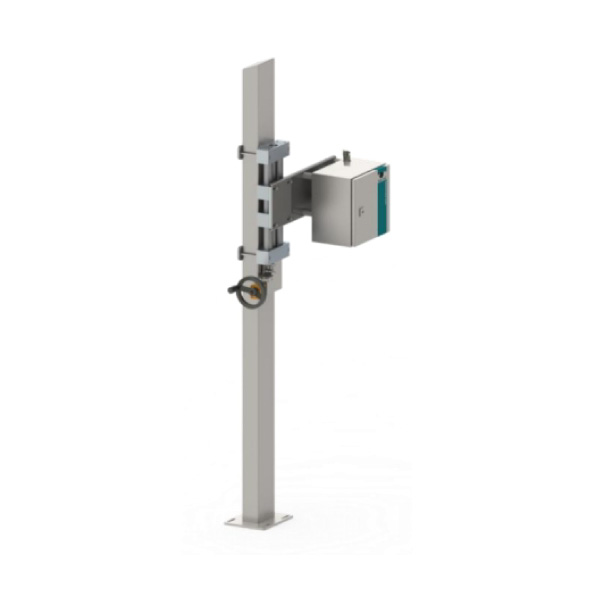
Code Inspection
The Code Reading modules inspect ink-jet, laser and thermal-transfer codes on various packaging types, including infant formula cans, food cans,beverage cans, labels, cartons, film, foil and PET bottles. The inspection checks if codes are present, complete, readable and correct.We deliver standard solutions ideal for High Speed performance, up to 2,400 cans/minute, as required in the beverage industry.
Options: Label ID numbers (MRDR code / OCR code), Fill-level Inspection, Serialization codes (unique code per product), etc.
Options: Label ID numbers (MRDR code / OCR code), Fill-level Inspection, Serialization codes (unique code per product), etc.
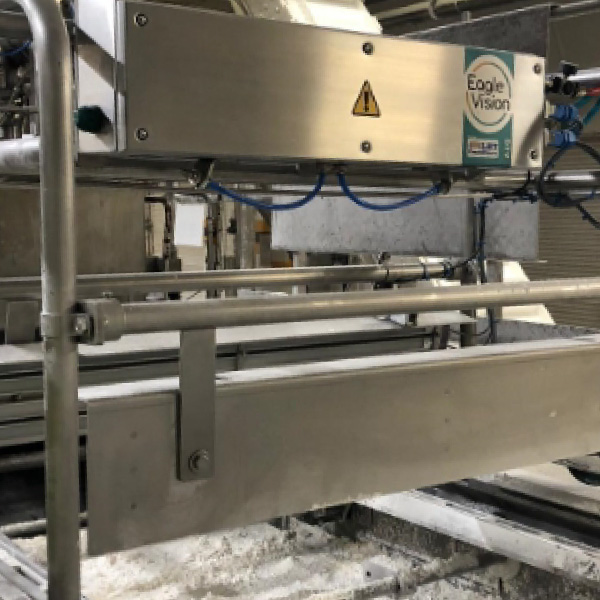
DTV Dirty Tray Vision System
The Dirty Tray Vision System is the innovative solution to prevent bad imprints and dirty trays in starch moulding production lines. The system is the result of a successful collaboration between Eagle Vision Systems and Luuk Hilhorst of LHT Consultancy. The Dirty Tray Vision System, DTV in short, inspects each and every tray immediatelyafter printing in the starch, before it will be filled with the liquid jelly. If the tray is not perfectly filled with starch or the quality of the imprint is not correct, the tray will remain in the line but will not be filled with liquid jelly and will therefore eliminate the risk the tray to get contaminated with hardened pieces of jelly.
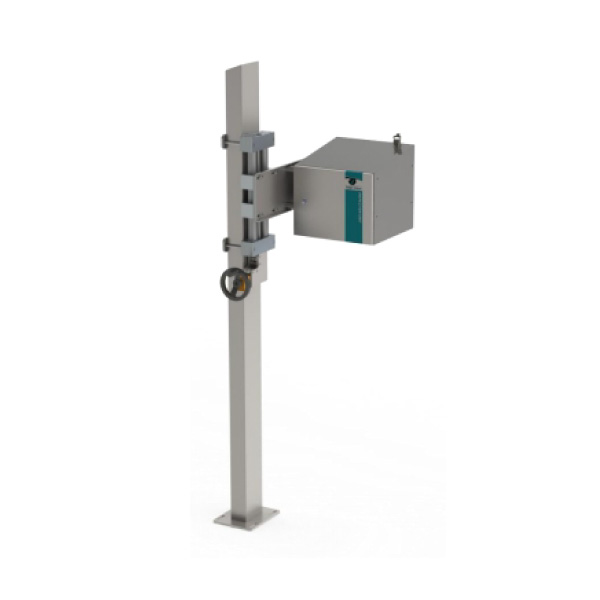
Empty Can Inspection
The Empty Can Inspection system is able to detect defects quickly and accurately on the flange, bottom and the inner sidewalls of the can. Pollution and spots inside, as well as flange dents, flange width and ovality/roundness are being inspected. The Empty Can Inspection system is available for high speeds. The example of inspection of flange is damages, dents, flange width and ovality/roundness. The inner bottom and inner sidewall is pollution, spots, damages and foreign objects
Options: 360° Can Inspection on the outside of the can, Seam Inspection
Options: 360° Can Inspection on the outside of the can, Seam Inspection
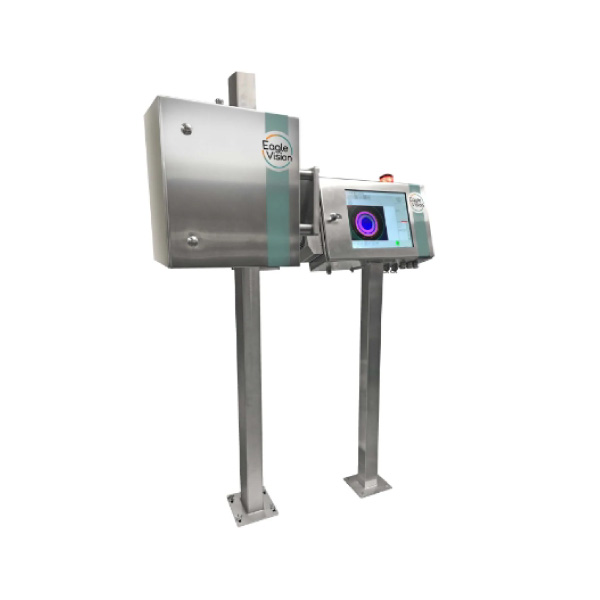
Metal Ends Inspection
The Metal Ends Inspection module inspects damages, roundness and compound on metal can ends. This includes scratches, dents, rust,contamination, compound misapplications and more. The system is available for high speeds and for several metal can end sizes and types.A key feature of the Metal Ends Inspection unit is the three colored light smart technology for identify product defects. Each light color is optimised to identify specific types of defects, allowing for sophisticated and convenient quality assurance checks. Blue Light – Optimised for identifying stains or scratches to coatings that expose metal Green Light – Optimised for dents and dust particles. This light technology is also ideal for inspections of compound applications. Red Light – Optimised for identifying scratches and dents with height information. This light technology is also ideal for inspecting the curl.
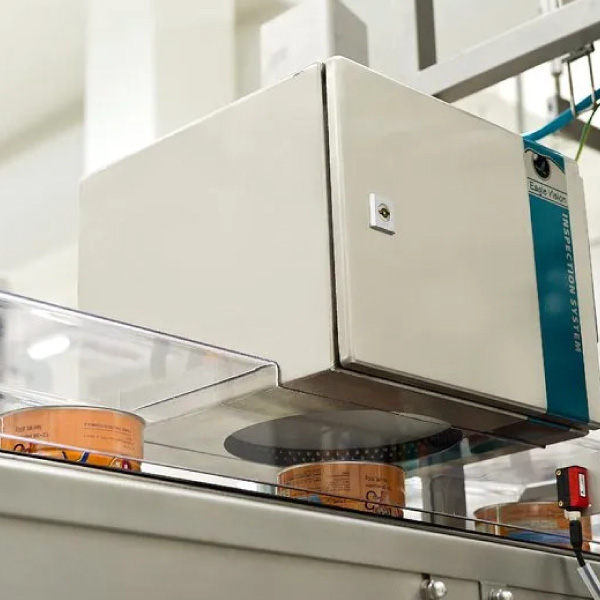
Scoop Inspection
The Scoop Inspection module inspects very accurately the scoop presence, broken scoops, double or multiple scoops and mixed-up/incorrect scoops by color. The Scoop Inspection module is also able to inspect white and transparent scoops.
Options: Empty Can Inspection (flange + internal can), Seam Inspection, 360° Inspection, (Spoon-) Cap Mix-up Detection: by color, label, embossing, Cap Orientation
Options: Empty Can Inspection (flange + internal can), Seam Inspection, 360° Inspection, (Spoon-) Cap Mix-up Detection: by color, label, embossing, Cap Orientation
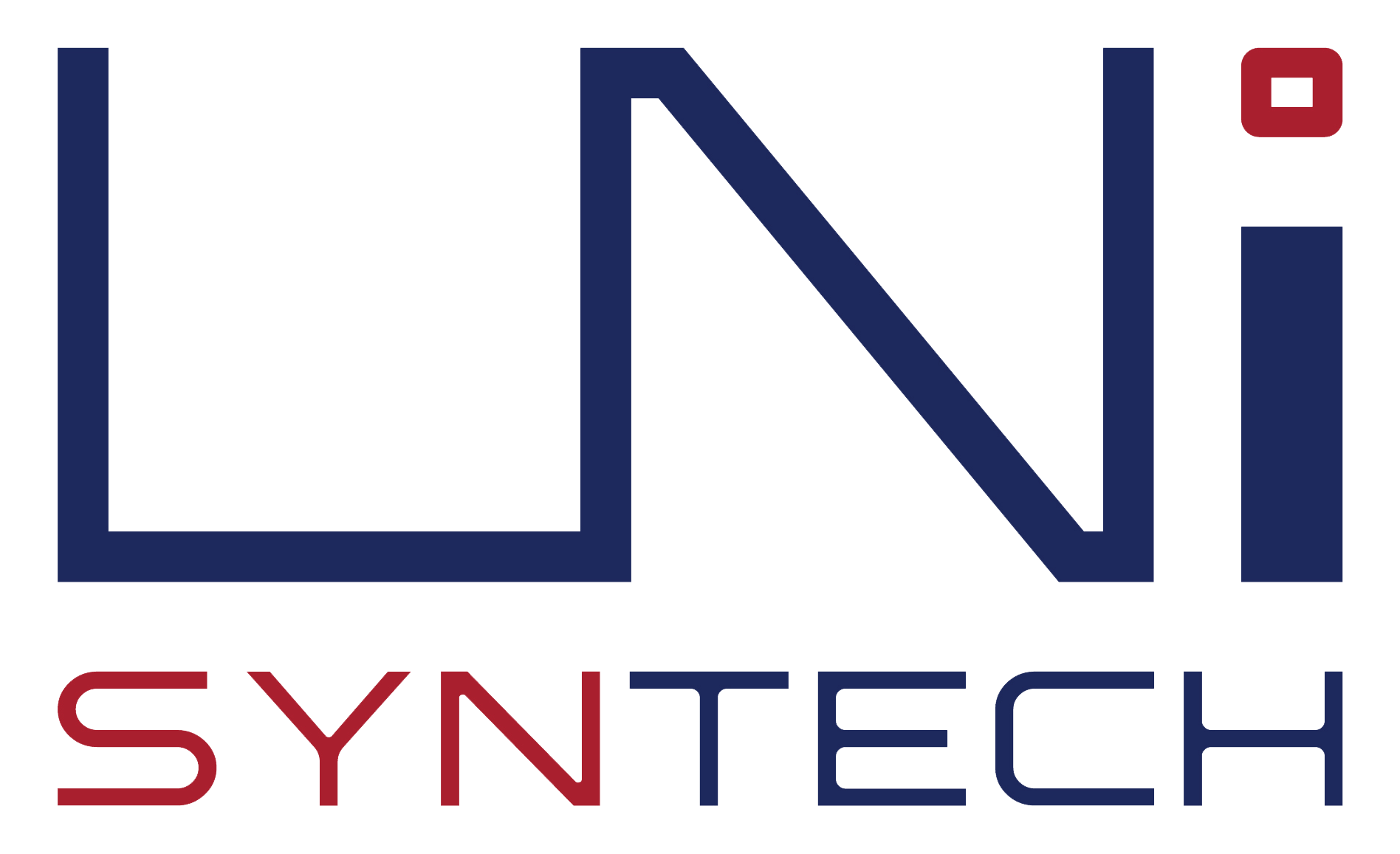
Head Office :
107/69 Moo 6, Khu Khot, Lam Luk Ka District, Pathum Thani 12130
E-mail : [email protected]
Mobile: Office 02-1026862 Sales 086-7888414
Line : @unisyntech
Facebook : Unisyntech Packaging Solution.